Corporate
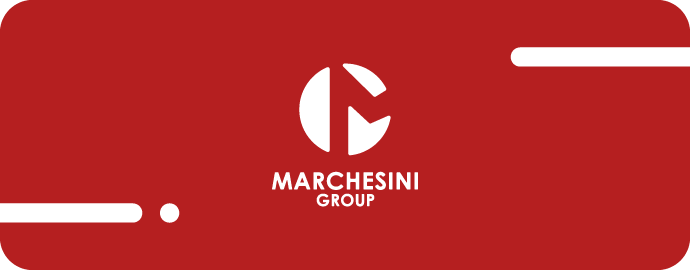
Le macchine della Serie Compact sono dei monoblocco tutto in uno per il riempimento e tappatura di flaconi per compresse, capsule o pillole nei. La Serie Compact è cartterizzata da un cambio formato facile e veloce ed perfetta per lavorare con diversi prodotti e quantità in lotti piccoli o medi. Il modello Compact24 usa un sistema di trasporto magnetico all’avanguardia che gestisce ogni flacone in modo indipendente, migliorando posizionamento, raggruppamento e velocità.
Caratteristiche principali:
OUTPUT | |
---|---|
Bottles/min: | Up to 200 |
Ricevi la brochure della macchina in formato pdf, direttamente nella tua casella di posta.