Corporate
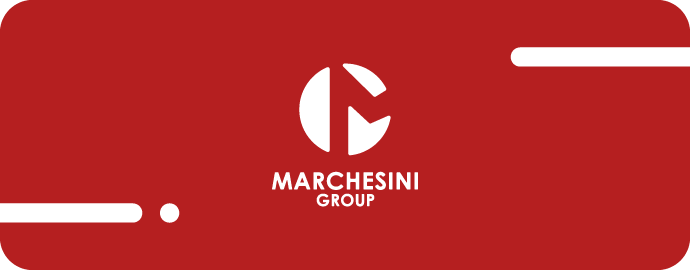
From the perspective of the Marchesini Group, environmental responsibility is expressed by means of an all-embracing approach aimed at preserving natural resources, attempting to avoid wastage, construed in the broadest possible sense, and offsetting it with recycling, responsible purchase and use of materials for a far reaching eco-compatible vision aimed at minimising environmental impacts connected to its business operations.
The company is therefore committed to the constant search for the most suitable solutions to guarantee responsible use of resources and a reduction of energy consumption through the ongoing improvement of its environmental performance, promoting the engagement and awareness raising of the entire management structure and workforce in a culture of shared responsibility, supplying the necessary resources and training. First of all, the Group aims to guarantee respect of statutory environmental legislation in all matters concerning
its internal operations. The Group also aims to collaborate with the Public Authorities and develop relationships of reciprocal trust with employees, customers, suppliers and, by monitoring environmental parameters, the organisation sets the ultimate goal of reducing all forms of pollution and environmental impact in line with its growth targets.
In particular, the organisation undertakes to:
• adopt all preventive approaches available to reduce pollution;
• optimise consumption of energy resources;
• use exclusively electricity generated from renewable resources;
• guarantee compliance with statutory legislation by the entire organisation;
• award priority to waste management companies committed to recovery/recycling;
• adopt the appropriate corrective/preventive actions whenever the need arises;
• disseminate a culture of sustainability and environmental respect throughout the entire organisation.
In line with the Environmental Policy, the Group bases its strategic action on three pillars:
SAVING NATURAL RESOURCES
Producing better, consuming less energy and fewer resources, optimising management of environmental aspects (resources, water, waste, raw materials) to leave future generations with a less impoverished and more viable environment. The commitment assumed is to revise Marchesini products, redesigning and studying them to reduce their environmental impact in terms of longer duration, greater flexibility, energy saving, and enhanced recyclability of components.
REDUCING THE IMPACT OF PRODUCTION SYSTEMS
Marchesini Group has made a commitment to review and re-design processes and technologies that prevent and/or reduce environmental impact. This will be possible only by applying the best operating techniques and guaranteeing rational and efficient use of energy resources and raw materials.
LEGISLATIVE COMPLIANCE
Marchesini Group's undertaking to comply with environmental legislation constitutes a mandatory step and it is also an expression of the maturity reached by the production plants and the MG governance system, guaranteeing sustainable use of natural resources and waste management. Compliance with the applicable statutory legislation and the assessment and implementation of proactive projects on these topics is entrusted to the Environment and Safety Department. 36 The data shown in this section are referred to Marchesini Group S.p.A.
The aereal view of January 2020 shows the recent enlargement of Pianoro's Headquarters including the Beauty
Virtuous behaviours are promoted throughout the Group aimed at reducing energy consumption linked to the daily requirements of
employees for their work activities; in addition, investments have been ongoing on devices capable of reducing wastes, e.g. during shutdown periods (night-time, weekends, public holidays), and high energy efficiency plants, also in replacement of low efficiency legacy systems.
The electricity used by the Group is mainly linked to feeding production cycles in the plants and, to a lesser extent, to offices and services. Total electricity consumed in 2020 corresponds to around 1,838 Toe37, up by around 1.4% with respect to 2019. The increase is mainly connected to the company’s growth and the gradual decommissioning of gas fired heating systems in favour of heat pumps.
The undertaking to provide the most people-friendly workplace possible38 with maintenance of microclimatic
comfort conditions (heating and air conditioning) in all the Group's manufacturing plants and offices, accounts for
around 50% of total energy consumption.
Total energy consumption in terms of toe (tonnes of oil equivalent) in 2020 was almost unchanged with respect to 2019 (+0.4%): the rise in electricity consumption due to the increase in production and employees and extension of factory space was offset by the reduced use of the fleet of company cars due to the pandemic.
Conversely, emissions in terms of equivalent tonnes of carbon dioxide were reduced overall to zero. This was possible thanks to the achievement of the goal of using exclusively electricity generated from renewable sources.
Higher efficiency in the use of materials in production processes translates into reduced costs, fewer waste materials sent to landfill,
and less processing scrap, all resulting in beneficial effects on the environment.
For these reasons, the Group promotes responsible management of materials and waste, with special attention devoted to the treatment and disposal of hazardous wastes.
The Environment-Safety Department is responsible for guaranteeing compliance with statutory legislation concerning the management of storage, transport and disposal of hazardous and non-hazardous waste. In the context of ongoing improvement and efficiency upgrading of production systems, Marchesini Group maintained the proportion of waste consigned to landfill to below 10%, increasing the recovery proportion accordingly.
Even though it does not use large quantities of water in its production cycles, the Group is committed to developing strategies to improve responsible management of water in recognition of the importance of this precious resource for the well-being of the general population.
Water resources management is handled by the Maintenance, safety and environment department which, among many other activities, provides legal support for the implementation of relevant new standards and regulations.
Use of water resources is largely the result of normal consumption for domestic hot and cold water uses. With regard to production, water is mainly used for wash-downs during machine testing and commissioning procedures.
To date, the water used in the production process is consigned to specialised recycling companies for disposal. Water withdrawals in 2020 totalled 30,323 m3, with an increase of 17% compared to the 2019 value, due to the increase in the workforce and the surface area occupied by the Company.
The Product Carbon Footprint (PCF), expressed in tCO2eq, considers total emissions of all phases of the product/service life “from cradle to grave” in relation to the Global Warming Potential of carbon dioxide (CO2).
PCF value calculation starts from the constituent materials procurement and treatment phase, proceeding to consider material processing phases and article production, up to transport to the customer and even extending, when relevant, to cover product use and disposal.
The company carried out the study in order to:
• identify the significant aspects in terms of climate change effects of the factories included in the company
perimeter in order to reduce and/or mitigate them;
• monitor variations in climate related impacts;
• the study considered all direct emissions (Scope 1) and indirect emissions (Scope 2)42 of greenhouse gases
associated with the factories included in the scope of the study.
Data collection was carried out using the following methods:
• preparation of forms to collect the processed data divided according to the different Scopes;
• coordination and discussion meetings at the Pianoro headquarters (BO);
• requests for additional information and data by means of telephone contacts or emails.
With regard to the greenhouse gas emissions of an organisation, the GHG43 Protocol classifies GHG emissions under three headings:
• scope 1: direct GHG emissions from owned or controlled sources;
• scope 2: indirect GHG emissions from the generation of purchased electricity or the portion of electricity
self-produced and consumed;
• scope 3: all other indirect GHG emissions not within scopes 1 and 2.
Since the measurement of emissions in this latter category is currently not mandatory but rather at the discretion of the organisation, the survey was restricted to scopes 1 and 2, for which the activity data were established based on information in utility bills or company fleet fuelcards.
2020 was accompanied by a 25% overall increase in emissions due to the leakage of refrigerant gas caused by the failure of several aid conditioning systems.
On the other hand, emissions due to electricity generation continue to be reduced to zero due to the exclusive use of electricity from renewable sources also in 2020.
The sense of responsibility towards the environment, combined with the desire to offer customers an affordable product with the same quality and reliability levels as new products, is certified by the third year of activity of Rinova S.r.l., the Group company set up to refurbish used original Marchesini Group machines and lines.
Starting from a used original component, subjected to a process of dismantling, cleaning, regeneration, refitting and final testing, the Group can bring new life to previously used machines, resulting in multiple benefits for customers. In terms of savings, prices are reduced by as much as 50% compared to a new component and, as for the other components, also regenerated replacement parts are covered by a 100% warranty and offer the same quality and reliability specifications. The recovery of previously used components is also a gesture of respect and awareness for our environment because it leads to savings in energy consumption and reduction of waste.
Remanufacturing is therefore not just a new production paradigm, but also a new business model based on the “second life” of materials, which can potentially make the production of assets more advantageous in economic and environmental terms.
The practice of remanufacturing involves disassembly of the used product and restoration by replacing components in order to preserve the original design specifications; for the consumer the resulting product must be considered on a par with a new machine.
In remanufacturing, the original added value of the raw materials used for the first version of the product, is regenerated.
Remanufacturing is defined by three main factors; firstly, the useful life of products is extended thanks to maintenance, regeneration, repair, and upgrading processes. Secondly, these products can be easily disassembled in order to replace or refurbish components as required, and to protect the recyclability and reusability of the materials. Finally, the value added, in terms of manufacturer, energy, and materials, can be completely recovered.