Corporate
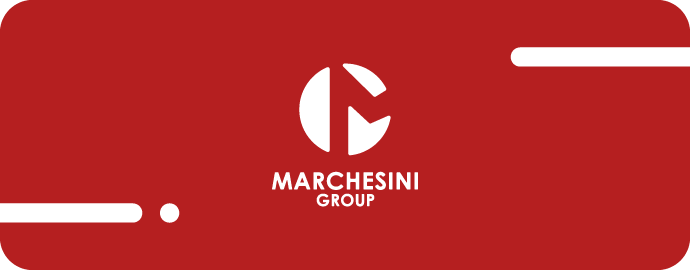
In line with the Environmental Policy, the Group has identified the following strategic guidelines:
Marchesini Group is committed to improving its production processes, consuming less energy and fewer resources, and optimising environmental management (resources, water, wastes, raw materials) to leave a less impoverished and more habitable environment for future generations. The commitment assumed is to revise Marchesini products, redesigning and studying them to reduce their environmental impact in terms of longer duration, greater flexibility, energy saving, and enhanced recyclability of components.
Marchesini Group has made a commitment to review and re-design processes and technologies that prevent and/or reduce environmental impact. This will be possible only by applying the best operating techniques and guaranteeing rational and efficient use of energy resources and raw materials.
Marchesini Group’s undertaking to comply with environmental legislation constitutes a mandatory step and it is also an expression of the maturity reached by the production plants and the Marchesini governance system, guaranteeing sustainable use of natural resources and waste management. Compliance with the applicable statutory legislation and the assessment and implementation of proactive projects on these topics is entrusted to the Environment and Safety Department.
Considering the multiple elements making up the Group’s technological solutions, the quality of supplies constitutes an essential aspect for the development of reliable products.
Marchesini Group adopts a responsible approach in order to manage the entire procurement chain, from small local businesses to large multinationals, creating relationships that extend beyond the sphere of mere sales transactions and promoting lasting and mutually beneficial collaboration with the most qualified partners who share the company’s principles.
It is in the Group’s interest to employ appraisal tools to check the fitness of vendors in view of the continuity of the business relationship; this attention is expressed both on the ethical level and in relation to matters linked to the quality and safety of products. For this reason, relationships with vendors are developed in complete transparency, based on the matters defined by the General terms of supply applied to all contracts, by any qualitative provisions, referenced directly in the orders and regarding activities that the vendor must perform to assure finished product quality, and by the Code of Ethics, which includes specific references to respect for human rights, environmental protection and workers health and safety.
Raw materials
In 2019 the main raw materials consumed totalled around 495 thousand tonnes, reflecting an approximate reduction of 10% with respect to the prior year.
In 2019 raw materials consumption was lower due to the downturn in production of the Neri division. It is however well understood that historic consumption trends have never been constant and have always followed a classic sinusoidal wave path.
Considering the specific gravity of wood to be 300 kg/m3, it was possible to calculate the quantity of material consumed in 2019 and 2018 in kilos, comparing the values obtained and shown in the table below.
Consumption of timber packing materials fell compared to the prior year thanks also to the decision to use metal loading units for the automated warehouse. Doubling of plant capacity, which took place in 2019, helped to reduce the number of timber pallets.
With regard to PET film, essentially bubble wrap, the increase recorded in 2019 is due to operations of modernising the warehouse, which made it necessary to re-register more than 33 thousand items that were moved from the old stores to the new vertical warehouses.
The 3D printers in the prototyping department use metal powder and ABS filament feedstocks, whose 2019 consumption is shown in the table hereunder.
The Group has continued to promote the principles shared with the Code of Ethics in selecting vendors, using its utmost diligence to check the origin of materials and the processing methods adopted: as soon as a supplier establishes a relationship with the Group, in addition to the requirements set down in the Quality Manual and by the technical specifications, it will be expected to share the Group’s values.
In 2019, a total of 67 audits were carried out on suppliers’ sites, two of which repeated after initially returning a negative result.
Moreover, during the year Marchesini Group adopted a Policy on sustainability of goods and services procurement, the aim of which, in line with the Code of Ethics, is to steer all Group Companies towards more responsible, ethical and sustainable procurement solutions, involving the entire production process upline chain in all contexts, from labour conditions to environmental impact.
Virtuous behaviours are promoted throughout the Group aimed at reducing energy consumption linked to the daily requirements of employees for their work activities; in addition, investments have been ongoing on devices capable of reducing wastes, e.g. during shutdown periods (night-time, weekends, public holidays), and high energy efficiency plants, also in replacement of low efficiency legacy systems.
The electricity used by the Group, exclusively generated from renewables since 2018 (link to headline) is mainly liked to feeding the plant production cycles and, in a smaller percentage, to offices and services. Total electricity consumed in 2019 corresponds to around 1,812 Toe, up by around 19% with respect to 2018. Increases are mainly linked to the higher number of machines produced and the inclusion of consumption.
The undertaking to provide the most comfortable possible workplace also by maintaining comfort (heating and air conditioning) in all the Group’s manufacturing sites and offices, accounts for around 50% of total energy consumption.
In 2019, total energy consumption in toe (tonnes of equivalent oil) rose by around 16.2%, due to the rise in energy consumption caused by an increase in production output, employees, the fleet of company cars (and their use) and gas for heating due to the extension of plant surface areas.
Conversely, emissions in terms of equivalent tonnes of carbon dioxide were reduced overall to zero (link to carbon footprint). This was possible because the goal of using exclusively electricity generated from renewable sources has now been achieved.
Higher efficiency in the use of materials in production processes translates into reduced costs, fewer waste materials sent to landfill, and less processing scrap, all resulting in beneficial effects on the environment. For these reasons, the Group promotes responsible management of materials and waste, with special attention devoted to the treatment and disposal of hazardous wastes.
The Environment-Safety Department is responsible for guaranteeing compliance with statutory legislation concerning the management of storage, transport and disposal of hazardous and non-hazardous waste. In the efforts to ensure continuous improvement and streamlining of the production systems, Marchesini Group has reduced the portion of wastes sent for disposal to below 10%, increasing the recovery phase.
The sense of responsibility towards the environment, combined with the desire to offer customers an affordable product with the same quality and reliability levels as new products, led to the incorporation of Rinova SrL, the Group’s subsidiary set up to refurbish used original Marchesini machines and lines. Starting from a used original component, following a process of dismantling, cleaning, regeneration, refitting and final testing, the Group can bring new life to used products with multiple benefits for customers. In terms of savings, prices are reduced by as much as 50% compared to a new part and, as for the other components, also regenerated replacement parts are covered by a 100% warranty and offer the same quality and reliability specifications as a new product. The recovery of previously used components is also a gesture of respect and awareness for our environment because it leads to savings in energy consumption and reduction of waste.Most of the Group’s waste products comprise materials used for testing in the production cycle of automatic machines and consist of miscellaneous packaging, paper packages and pharmaceutical products (mainly placebos).
Conversely, waste fluids, exclusively from the part washing process and cold machining operations, are stored and then disposed of in compliance with statutory regulations. No waste fluids are released into drains or sewers.
Even though it does not use large quantities of water in its production cycles, the Group is committed to developing strategies to improve responsible management of water in recognition of the importance of this precious resource for the well-being of the general population. Water resources management is handled by the Maintenance, safety and environment department which, among multiple activities, provides legislative support for the implementation of new standards and regulations in this area.
Use of water resources is largely the result of normal consumption for domestic hot and cold water uses. With regard to production, water is mainly used for wash-downs during machine testing and commissioning procedures. To date, the water used in the production process is consigned to specialised recycling companies for disposal.
Water withdrawals in 2019 totalled 25,982 m3, essentially in line with the 2018 value. The stability of this value, despite the increase in the Company’s workforce and total surface area occupied, was achieved by reducing distribution network and irrigation system losses.
The Product Carbon Footprint, expressed in tCO2eq (Carbon Dioxide Equivalent tonnes) considers total emissions of all phases of the product/service life “from cradle to grave” in relation to the Global Warming Potential of CO2. PCF value calculation starts from the constituent materials procurement and treatment phase, proceeding to consider material processing phases and article production, up to transport to the customer and even extending, when relevant, to cover product use and disposal.
In relation to the greenhouse gas emissions of an organisation, the GHG[1] Protocol classifies GHG emissions under three headings:
Since the measurement of emissions in this latter category is currently not mandatory but rather at the discretion of the organisation, the survey was restricted to scopes 1 and 2, for which the activity data were established based on information in utility bills or company fleet fuelcards.
Specifically, the highest contribution to the total is related to indirect emissions resulting from use of company vehicles (40.6% of total) and natural gas consumption for heating (39.7% of total).
In contrast, emissions for electricity generation have been reduced to zero.