Corporate
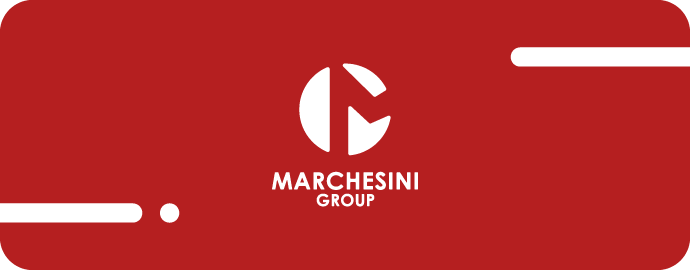
A unique sector prototype enables the production of filtration materials for face masks with greater protection against viruses and bacteria compared to materials currently in use. The technology was created by a multidisciplinary research group at Bologna University in collaboration with Marchesini Group. The researchers are now finalising the development of the machine, which should be fully operational in the space of a few weeks.
“The prototype enables industrial-scale production of this new type of filtration material, based on electrocharged polymer nanofibres”, explains Andrea Zucchelli, a professor with the Department of Industrial Engineering at Bologna University, and one of the project coordinators. “We embarked on a co-design operation in partnership with Marchesini Group, which responded to an appeal we launched in Bologna, and in under two months, thanks to vital teamwork, we came up with this machine”.
Once up and running, the prototype, which is housed in the laboratory of the Department of Industrial Engineering (DIN) in Bologna, will produce enough filtration material for around seven thousand masks per day. The first production runs of these materials will be used to produce a prototype batch of FFP3-type masks by Zola Predosa-based company GVS, a leader in the supply of advanced filtration solutions for highly critical applications and a major world producer of personal protection equipment, which has been involved in the project from the outset.
It all began shortly after the start of the coronavirus outbreak: given the huge spike in demand for appropriate personal protection equipment, an interdisciplinary research group at Bologna University set about developing a filtration material that would offer high protection against the risk of contamination from bacteria and viruses. The group was led by professors Andrea Zucchelli of the Department of Industrial Engineering, Maria Letizia Focarete of the "Giacomo Ciamician" Department of Chemistry and Davide Fabiani of the "Guglielmo Marconi” Department of Electrical, Electronic and Information Engineering.
“Only a University environment could nurture and support a project of this kind, designed to rapidly and effectively combine notions from the fields of mechanical engineering, polymer research and electrical engineering to develop an advanced electrospinning technology”, states Zucchelli. “Thanks to this synergy, we succeeded in combining electrospinning technology, which allows us to produce material with nanometric fibres, with corona discharge, thanks to which we were able to obtain nanofibres with a high electrostatic charge”.
“This project is the result of an invaluable, consolidated collaboration between Marchesini Group and Bologna University, pursued without interruption at a time of great difficulty for the regional and national economy” adds Maurizio Marchesini, Chairman of Marchesini Group. “Together with connectors for face masks which we produced using 3D printing technologies, this prototype further demonstrates how technology can also be used to meet society’s needs, both during this pandemic and afterwards”.
This new material offers great advantages when used for protective face masks: it retains airborne particulates containing viruses and bacteria, blocking them far more effectively than more commonly used materials. Moreover, it has an excellent particle filtration capacity, and can be applied to fabrics not normally used to produce face masks.
“We have a keen interest in developing and using innovative materials that allow us to bring the market personal protection equipment with enhanced safety and comfort for end users” comments Massimo Scagliarini, CEO of GVS. “The partnership with Bologna University allows GVS exploit and expand its know-how in the field of filter materials, promoting local synergies and using local sources to help supply production lines for FFP3 masks, which GVS has swiftly produced in Italy to deal with the pandemic”.
However, after developing and testing the technology needed to create these innovative polymer nanofibres, the production phase beckoned. The research group appealed for a manufacturer capable of producing the essential components and Marchesini Group responded, teaming up with Bologna University. The University research group and the technicians of the Bologna-based company set to work: in the space of a few weeks, the machine was ready.
One of a kind, the prototype will be fully operational shortly, as soon as the final set-up activities are completed. The first masks to be produced will be of the FFP3 type, offering ultra-high protection against viruses and bacteria, but the researchers are already working on new ideas to further broaden applications of this new technology.