Corporate
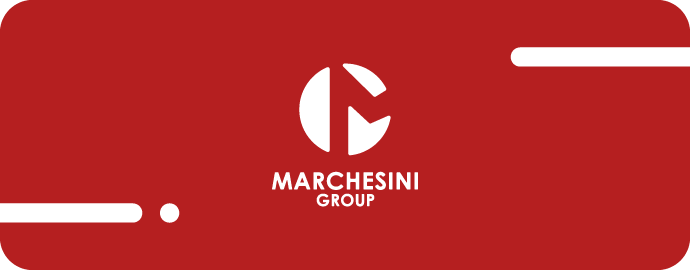
One of the novelties on show at Achema is the robotic blister line Integra 320, which has been especially set up to meet all the needs of every customer in terms of integration 4.0. This worldwide preview of the machine at the venue in Germany includes the 5-camera infeed system Valida, which provides multivision control of pill shape, thickness and colour, as well as a Near Infrared system (NIR) that recognises the active ingredient.
The machine is equipped with a new SCADA system, which has been developed together with SEA Vision, a leading company that creates vision and inspection systems that has recently joined the Marchesini Galaxy. The SCADA system constantly monitors the quality parameters and provides operators with feedback on the mechanical and functional state of the machine. To conclude, the line is rigged out with a predictive maintenance system that recognises any kind of mechanical error and suggests what programmed maintenance work is needed.
The end result is a combination of the consolidated strongpoints of Integra 320 and the integration novelties of Industry 4.0, forming a packaging line in which all the systems are integrated and perfectly linked to each other.
The line’s infeed speed is about 3000 pills per minute, meaning up to 320 blisters and 260 cartons a minute.
The pre-feeder upstream from the line exploits a new “Multivision” system that checks the integrity of the pills. This patented artificial vision system consists of the following:
Thanks to these sophisticated vision systems, Valida is able to detect the thickness and consequently eliminate any pills that are broken in half or that have one part totally intact but the other partially or totally missing. In such conditions, any other conventional camera that detects the product just from the top would not be able to detect these errors or would just give the signal to reject the whole blister. The pre-feeder therefore does indeed cut down on wasted product and wasted packaging material, which improves the existent efficiency of Integra 320 even further.
The second novelty onboard is a system that checks the active ingredient of the pills. Detecting the same shape and colour, it can distinguish a product that is the same but of different dosage or a product that is completely different, consequently rejecting the blister with the “wrong” pill inside it. The machine also has a Harlequin blister control system to check if the blister is complete.
The SCADA system, developed jointly with SEA Vision, constantly monitors the quality parameters and informs the operators on all of the machine’s operational parameters. It acts as a real data collection system for the line and as a “collector” for the various vision systems.
The predictive maintenance system works right across the whole line. It communicates with the SCADA system and is able to recognise every kind of mechanical error and to suggest programmed maintenance actions.
Predictive maintenance is one of the most complex yet interesting challenges of Industry 4.0. It allows customer to detect and store the data collected by machine sensors and provide specific feedback in order to create a “Log” database to which Machine Learning analyses can be applied. Installed on Integra 320, the predictive system will also allow customer to extend and maximise the service life of the machine, measure performance and suggest maintenance only when it is really necessary, thus doing away with unneeded work and improving overall production efficiency.