Corporate
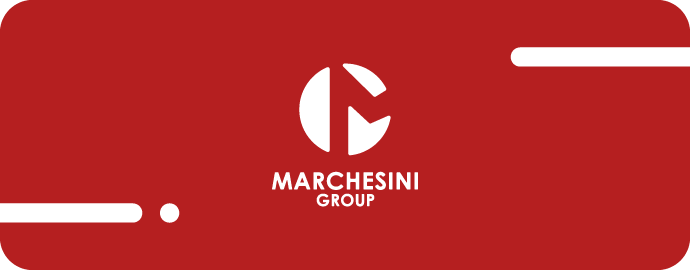
SEA Vision systems offer a wide range of controls for labelling machine from codes and variable data control to printed quality verification of the artwork and label presence, correct position and application on product.
They are installed directly on the labelling machines and analyze in real-time 100% of the products (not statistic control) also at high speeds. One or more controls are performed simultaneously.
The system is composed by hardware (Industrial PC, cameras, light units) and software (with advanced proprietary algorithms) perfectly integrated with the Marchesini Group packaging machines.
Camera optics and light units are selected for optimal image acquisition. The results are always optimal, even in case of labels realized with special materials as, for example, reflective and glittered surfaces. The setup is expandable and capable to control the correctness of different labels on the product.
All the computations are performed at very high speed and the result is communicated to the machine to reject automatically the defective cartons without affecting the production speed.
HARDWARE | |
---|---|
Industrial PC | |
Camera and light unit optimized for the control to be performed | |
Separated touch screen display (optional) or integration with Marchesini machine HMI | |
SOFTWARE | |
Windows 10 operative system | |
SEA Vision software with proprietary algorithms for performing controls and machine integration |
Print management and control of 1D and 2D codes on label as for example QR code, Data Matrix, Pharmacode, EAN code. ANSI Grading control in real-time to assure the printed quality of the code.
Print management and control of variable data on label like production date, batch number, expiry date and other.
Control of label artwork printed quality. Control of the presence of single graphic element inside the artwork.
Control of the shape and of the position of the bottle using dedicated cameras for correct pre-orientation before label application.
Control of label presence and correct position on the bottle. The system identifies correct alignment, rotation and position measuring the distance between specific points and avoiding skewed labels. Control of correct label adhesion and identification of defects like wrinkles, air bubbles and rips.
Receive the machine brochure in pdf format, directly in your e-mail inbox.