Corporate
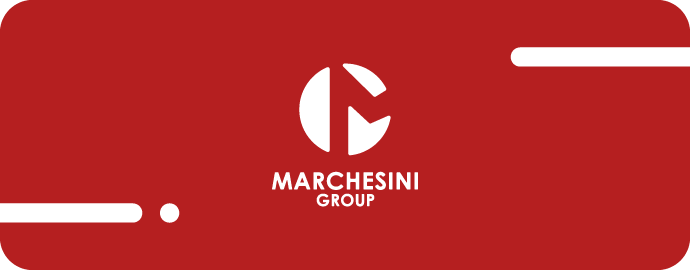
For over 10 years, Abbott Diabetes Care division has specialized in the production of glucose monitoring devices. As a part of one of the largest health care companies in the world, the organization is committed to bringing innovative technologies to people with diabetes, enabling them in better health.
Abbott recently launched its revolutionary FreeStyle Libre Flash Glucose Monitoring System, a small glucose sensor connected to a patch worn on the skin that offers continuous glucose monitoring for 8 hours once scanned. The sensor is disposable, water-resistant, and wearable for up to 14 days.
Because of the novel nature of the device, Abbott began researching packaging lines early in the development process. “We began looking for options as soon as the form factor for FreeStyle Libre was defined. Once we knew the major components, we began sourcing packaging solutions,” says Scott House, Division Vice President, Global Worldwide Operations at Abbott’s Diabetes Care Division. “At Abbott, we are committed to excellence across all spectrums of health, including technology, innovation and science and with a revolutionary product such as FreeStyle Libre, it only made sense that we would look for leaders in innovation when it came to our partners as well. The Marchesini Group is known for revolutionizing the packaging industry and our partnership with them has enabled us to employ the latest technology”.
The FreeStyle Libre system consists of two major components that go into the packaging: the sensor and the applicator. “One of those components needs to be kept sterile, so maintaining a sterile barrier throughout the packaging process was a critical need for us,” House explains. “The packaging line also needed to be very high-speed to meet our ever-growing capacity demands. Being able to meet these critical needs for us was a key reason in us choosing Marchesini as our partner, along with their ability to meet our aggressive timelines”.
The FreeStyle Libre line, which runs at a speed of 60 parts per minute, consists of the following equipment:
Because the line is so specialized, customization was necessary. “The highly technical nature of FreeStyle Libre necessitated a completely bespoke front end of the machine, something neither Marchesini nor we had even done before,” explains House. “The machine design and development efforts had to be very closely coordinated to ensure the final outcome. This effort proved very useful in forming the relationship we have today”.
Marchesini equipped the line with a custom Windows-based line management system, which controls communication with all peripheral devices and manages product programming and tracking of each individual unit through the line. User interfaces are managed by Siemens PLCs, which feature useful equipment diagnostics. Line changeovers are limited to setting new Stock Keeping Units (SKUs) within the line management system, without requiring physical adjustment on the machines.
After a two-year design and development process, the line took approximately two weeks to install, which was followed by a vigorous validation process to prepare for production.
In production since 2014, FreeStyle Libre is changing the way users manage diabetes, giving patients the benefit of continuous glucose monitoring (CGM) with real-time glucose values and trend data. “From the beginning, our two groups worked as true partners in developing the footprint for this packaging machinery, both sides providing their insight and expertise until we reached the final - a product that achieves our objectives in packaging at scale, enabling us to bring this product to as many people with diabetes as possible,” House says. “Marchesini showed creativity and ingenuity in meeting our requirements; the build quality is excellent, and they fully supported us throughout entire process leading up to production - all of these things are critical to our success”.
*Author: Keren Sookne, Director of Editorial Content at Healthcare Packaging