Corporate
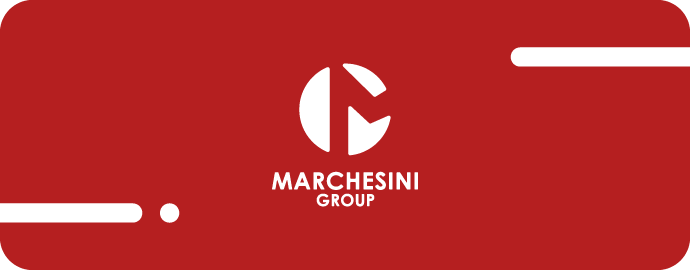
Marchesini Group Beauty together with SEA Vision offer a very wide range of controls on all the main types of squeezable tubes used by the cosmetic industry and made of plastic, paper and aluminum.
Vision systems check the complete correctness of the tube, its orientation and perfect closure, the correctness of the codes and of the variable data printed on it and avoid the presence of impurity before filling.
They are installed directly on the packaging machines and analyze in real-time 100% of the products (not statistic control) also at high speeds. One or more controls are performed simultaneously.
The system is composed by hardware (Industrial PC, cameras, light units) and software (with advanced proprietary algorithms) perfectly integrated with the Marchesini Group packaging machines.
All the computations are performed at very high speed and the result is communicated to the machine to reject automatically the defective units without affecting the production speed.
HARDWARE | |
---|---|
Industrial PC | |
Camera and light unit optimized for the control to be performed | |
Separated touch screen display (optional) or integration with Marchesini machine HMI | |
SOFTWARE | |
Windows 10 operative system | |
SEA Vision software with proprietary algorithms for performing controls and machine integration |
Control of the tube shape correctness before filling.
Control of the presence of foreign objects and impurity within the tube before filling.
According to the position of the codes or notch, the system exchanges a signal with the machine to correctly orientate the tube, ensuring perfect graphic artwork positioning.
Correct 2D codes control printed on the tube. The control includes ANSI Grading in real-time to assure the maximum quality of the code.
Tube sealing defect control, checking if the tube is completely or partially open or has wrong sealing or defects placed near the sealing area.
Control of the variable data printed on one or both sides of the tube.
Receive the machine brochure in pdf format, directly in your e-mail inbox.