Corporate
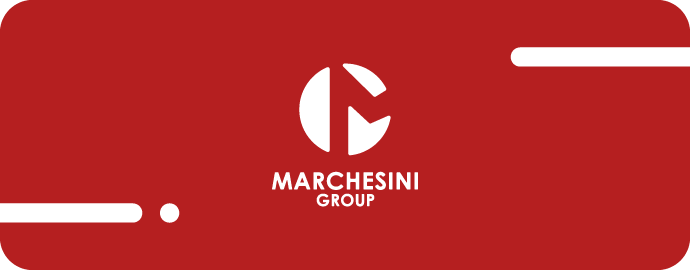
We were one of the first companies in the Italian packaging industry to install an automated storage warehouse to manage the entire service life of each machine as well as in-house production needs and spare parts requests from our customers.
This applies to the use of our robots on the machines too. But what really makes the difference is not actually the use of automated systems but the software we have developed and the customisation of the automated process itself. Robotics are not just used to manage standard products, but are exploited to develop highly customised projects and this has always been our mainstay. It goes without saying that in-house logistics too has to be organised in order to meet customers’ requests efficiently and to pinpoint a machine part rapidly and exactly, be it a part required for the production line or a spare part for customers. This is how we build customer fidelity. Quoting a theatrical term, we work “behind the scenes”; not much is visible but all is crucial to ensure the show’s success and positive interaction between the protagonists.
50 people work permanently at our logistics departments. They interact daily with 29 automated storage warehouses, which hold more than three million items. A huge Automated Storage and Retrieval System (ASRS) is installed in Pianoro. After the initial investment, this system helps us deliver the customer-designd units directly to the assembly line without error. Thanks to its secret algorithm, Arlecchino ensures us and our customers the following: