Corporate
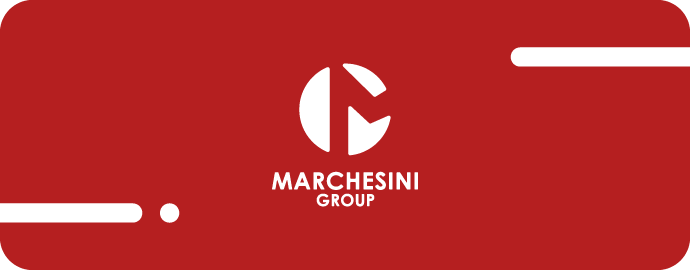
Hyper technological factories that produce pharmaceuticals sold in 20 countries of Latin America. Top quality raw materials and observance of standards to guarantee product safety. Strong investments in Research & Development to create medicines that all users can buy.
The world of Mega Pharma is variegated, complex and widespread since the company is organised on various bases of investments and future forecasts. In the site of the Parque de las Ciencias Free Trade Zone, which is a modern area of buildings that have been built not far from the airport of Montevideo, in Uruguay, Mega Pharma produces various ranges of generic medicines, from those used in cancer treatments through to those used to treat metabolic, pain, respiratory and skin diseases. It is a wide offer for customers of the pharmaceutical market, which has been made possible also thanks to a strategic alliance with other major pharmaceutical companies of Latin America, such as Roemmers, Rowe, Medihealth and PharmaInvesti.
Despite the large number of pharmaceuticals requested by an ample and developing market such as that of Latin America, the quality and the safety of the same are requisites that represent a good share of the core business of Mega Pharma. Supervision over quality and safety of the product has been made possible thanks to the use of a sophisticated Integrated Pharmaceutical Monitoring System that allows the company first of all to identify and assess the risk of the medicines sold, in order to implement measures capable of eliminating the foreseeable risks and of eliminating those unforeseeable, as far as possible. This system, which works also through a communication system aimed at promoting an appropriate use of the medicines, allows Mega Pharma to respect international standards on safety matters and also to interact constantly with the supervision authorities of the countries in which the medicines are sold.
At the Parque de las Ciencias, Mega Pharma is working to build the future of one of the most important pharmaceutical industries of Latin America. In the Free Trade Zone, there is the Mega Pharma Campus, in which the company has decided to invest 90 million dollars. In addition to the Headquarters, where the offices are located, the Campus is giving life to a new pharmaceutical factory, which will become the heart of the production centre. Not far away is the Research & Development centre of the company where a team works to develop new molecules, as well as all the systems necessary for logistics, which have been entrusted to Selenin, being the most important Pharmaceutical Logistical Operator focused on exportations in Uruguay. The Campus was devised and built as a self-sufficient village with low environmental impact interacting also with the local scientific community. The result is a company spread out across the territory working to expand across the world, also thanks to its project to find new commercial partnerships.
Mega Pharma has purchased four Integra 320 blister packaging lines from the Marchesini Group. This solution is the sister of the Integra 520 V line and is designed to separate the zones and to be time and cost saving. The new machine pitch control system, the new cartoning section and the innovative carton opening and product insertion system ensure very high production rates of up to 320 blisters and over 260 cartons a minute. The machine footprint is condensed thanks to the compactly devised blister thermoforming and carton packaging phases. A Robocombi with three axes and pick-up head with suckers patented by the Marchesini Group connects the two stations, consequently minimising size change-over operations. The units are no longer made up of lots of individual parts, but of integrated blocks, which can be replaced with just one movement.