Corporate
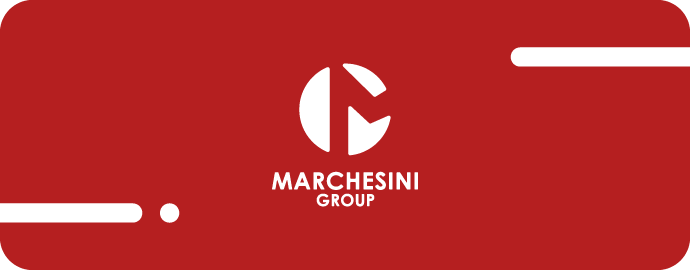
We set up a new 1,000 square meters building dedicated exclusively to the 3D printing of plastic and metal parts, in addition to combined plastic-rubber parts used in production and also as prototypes.
In addition to the 3D printers ā which work 24 hours a day, connected inline and programmable from our offices to work with the additive manufacturing method ā the department also houses laser cutting and automatic metal bending systems. Together, these special tools allow us to:
All without using a single sheet of paper.
Pursuing the same goal, we built the new Research and Development workshop, a 1,000 square meters space where the applications of the future are tested and trialled. This further investment will lead to more innovation, reducing product analysis times, with a view to meeting the faster delivery times that customers increasingly demand.
Our Research and Development is split into three macro areas:
Hardware: design, trialling & testing of new projects, including:
Software: development of innovative technologies and data collection algorithms to support design and physical production, including:
Alongside these two areas are numerous external collaborations with scientific organisations, Universities and research laboratories.