Corporate
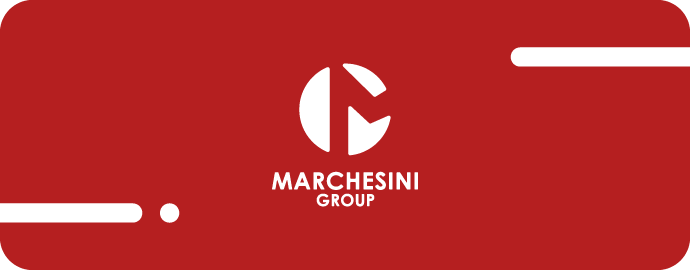
SEA Vision systems offer a very wide range of controls for liquid filling and capping machine: from product presence and integrity, 1D and 2D codes and variable data printed on the bottle to more specific controls as liquid level, mouth integrity and correct shape, detailed control on the cap and its components, presence of foreign bodies inside the bottle before filling.
They are installed directly on the filling and capping machine and analyze in real-time 100% of the products (not statistic control) also at high speeds. One or more controls are performed simultaneously.
The system is composed by hardware (Industrial PC, cameras, light units) and software (with advanced proprietary algorithms) perfectly integrated with the Marchesini Group packaging machines.
All the computations are performed at very high speed and the result is communicated to the machine to reject automatically the defective units without affecting the production speed.
HARDWARE | |
---|---|
Industrial PC | |
Camera and light unit optimized for the control to be performed | |
Separated touch screen display (optional) or integration with Marchesini machine HMI | |
SOFTWARE | |
Windows 10 operative system | |
SEA Vision software with proprietary algorithms for performing controls and machine integration |
Control of the presence and correctness of the product and of its integrity. The system identifies missing, wrong or broken components, body integrity and presence of defects like scratches.
Control of correct liquid filling level inside the bottle.
Print management and control of 1D and 2D codes (for example QR code, Data Matrix, Pharmacode, EAN code) on the product body or cap. ANSI Grading control in real-time to assure the printed quality of the code.
Print management and control of variable data like production date, batch number, expiry date and other, on the product body or cap.
Control of the integrity of glass bottle mouth.
Control of bottle integrity. Identification of glass fragments on the bottom.
Control of the shape of bottle mouth.
Control of the presence of the cap. Control of the correct closure by identifying and measuring specific points.
Control of the presence and position of sealing ring on bottle caps.
Control of sealing membrane under the cap, in order to verify its presence and position, the accurate sticking with the bottle neck and presence of flaws.
Control of the presence of spray caps and deep tube and their correct assembly, position and colour.
Control that the dropper tip hole is open and detects obstruction or flaws in a dropper tip hole.
Control of cap defects or missing part.
Control of correct crimping, cap and spray cap presence and position.
Receive the machine brochure in pdf format, directly in your e-mail inbox.