Corporate
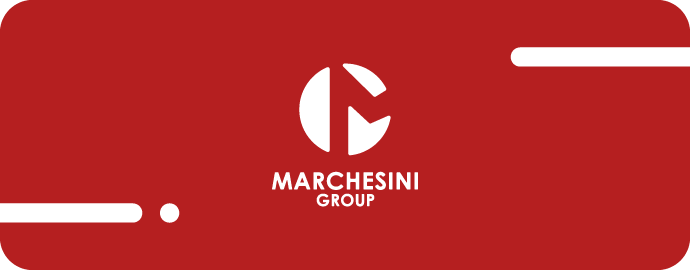
Extrafill is a filling and stoppering machine for syringes in nests, developed to meet the growing demand of packaging disposable pre-filled syringes. Extrafill is compact, flexible and designed to accommodate from two to five filling and stoppering stations and make it easier to manage the work areas.
Extrafill will be exhibited at Interpack as an innovative monoblock unit designed to combine tub opening and syringe filling/stoppering phases under just one RABS or isolator.
The outcome is a machine capable of producing up to 12 thousand pieces per hour, assuring incredibly precise operations, thanks to syringe and stopper handling systems able to prevent any possible contamination and ensure a perfect aseptic process.
Extrafill is equipped with rotating piston pumps and an innovative “Statistical In Process Control” weighing system, which offers economic and technical benefits compared with traditional solutions.
The machine exhibited at Interpack will have the tub opening (by means of a robotic peeler) and syringe filling/stoppering phases integrated all in one monoblock unit.
Once loaded on the machine, the tub passes under the warm-up system that heats the edges. The tub moves under the opening station where a robotic arm peels off the external Tyvek® lid and remove the internal protective film, discharging them onto a recovery extractable bin. The same robot transfers the open Tub on the load belt of the filing and stoppering unit.
Just one isolator (or RABS) protects both zones, but still separates them with vertical laminar air flows and individual pressure control on each area, to guarantee a correct pressure cascade typical of an aseptic filling process.
The isolator and the machine are sanitized by Vaporization of Hydrogen Peroxide (VHP). The VHP technique minimizes sterilization and aeration time.
The new monoblock can be equipped with peristaltic filling pumps and automatic filling volume adjustment controlled by the innovative Single Scale Statistical Weighing System, that - compared with traditional multiple scales solutions - offers economic and technical benefits, as the absence differential error during syringe weighing and a more compact footprint.
The heart of the machine: a new high-tech arm that moves just like a human hand
The robot that has been integrated in the new syringe filling unit is the outcome of research activities carried out by the Marchesini Group to innovate the automatic machinery industry.
Both the mechanics and software of the Tub de-liding head have indeed been developed entirely by the R&D team with the aim of devising a specific robotised system capable of handling the product with outstanding efficiency in sterile conditions. Since it has been purpose-designed for this function, the robot has been given a futuristic gripper that moves just like a human hand. The software is also incredibly effective in moving it and performing the various consecutive operations:
Phase 1 - handling: the robot get the tub and puts it into position;
Phase 2 - look for peel-off corner: this phase has been studied to mimic human hand movements. The robot looks for the corner of the lid to be lifted, also, or especially if the corner is folded or bent, and grasps it to gently remove the entire lid without tearing;
Phase 3 - peeling: the robot peels off the outer lid and throws it into the dedicated bin;
Phase 4 - remove second protective cover from tub: the robot uses its vacuum cup to get the second cover of the tub, removes and throws it into the collection bin;
Phase 5 - handling: the robot gets the tub again and carries it to the load conveyor of the filing unit.
Flexibility
The machine is easily integrated in various possible layouts and material flows thanks to the special design of the work areas. Special attention has been paid to designing the moving components, preferring the use of rotary drive shafts or linear drive shafts with open wheel, which are indispensable techniques to ensure machine cleanliness and integration of RABS or isolators, assuring a full air-tight separation of process area and technical area.
Precision and reliability
Optimization of the working phases and process parameter can be saved on the operator’s interface and re-loaded later as a “Product Recipe”. This is made easy thanks to the servomotors used to drive the movements of the machine.
Different optional are available for the filling system - such as steel or ceramic rotary piston pumps, peristaltic pumps, circuits for CIP/SIP or disposable dosing systems. In addition to dispensing precision, the machine also guarantees maximum protection of the syringes, which must not be damaged in any way during filling. In fact, the Extrafill machine avails of exclusive systems during syringe handling, filling and stoppering phases, which optimize centring, thus safeguarding the syringe barrels against the risk of breakage or damage.
Integrated weight control system
The machine has been enriched with the integrated weight control system (IPC). The IPC control system of the product weight filled in the syringes makes it possible to verify the tare weight (unfilled syringe) and the gross weight (filled syringe without stopper) using just one load cell for all filling station. Sampling can be performed once on each single nest and the frequency of controlled nests that can be chosen via the control system.