Corporate
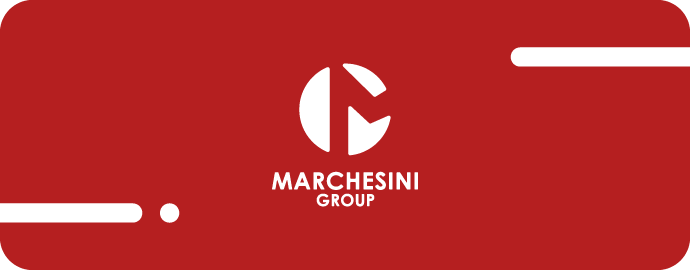
Amongst the biggest innovations the Marchesini Group will be showing at the Düsseldorf exhibition from 4 to 10 May will be a large area dedicated to sustainability and solutions for packaging pharmaceutical or beauty products with environment-friendly materials.
So visitors to the company’s stand of more than 1500 square metres (Hall 15 – Stand A42 1-6) will enjoy a close-up view of a number of machines and lines able to package products with different types of materials, including paper, recyclable and recycled mono-material plastics and aluminium. Each of these solutions is the outcome of research and development work directed at meeting the market’s demands: “More and more customers are calling us in for projects that involve the sustainability of packaging materials,” Group CEO Pietro Cassani tells us. “Good results in this area require a high degree of cooperation between ourselves as automatic machinery constructors and the suppliers of the packaging materials; the issue must be tackled with a holistic approach that considers all the requirements involved and increasingly embraces the packaging’s entire lifecycle.”
The stand will exhibit a machine designed to carton vials in paper trays. This solution is presented together with a new-design paper tray, researched and developed entirely by the Group itself, which generates savings of about fifty percent in paper and about fifty percent in glue compared to the models currently on the market.
What’s more, the new paper tray is less thick, providing space savings of thirty percent when products are combined inside the case, with obvious benefits during shipment in terms of load capacities and relative CO2 emissions. The Group, which has been developing paper tray solutions as a valid, safe alternative to thermoformed plastic for more than ten years, has created this new prototype with the aim of guaranteeing even more responsible use of packaging material, while further reducing production costs and avoiding waste.
Also on show in the sustainability area will be a complete line for blister products, comprising first and foremost an integrated, robotised solution which inserts tablets in a packaging consisting of seventy-five percent PVC-free aluminium, an entirely recyclable, infinitely reusable material, and then in a cardboard carton. The line is completed by a monobloc comprising a case packer and a palletiser equipped with an innovative robot.
Apart from the all-aluminium primary packaging, this line’s truly innovative feature is the installation on the machine of a Track & Trace technology by SEA Vision: from blister serialisation through to pallet aggregation, a single solution to protect the brand and safeguard the product against counterfeiting.
Visitors to the stand will also be able to view a thermoforming machine for forming mono-material trays in R-PET, PET containing up to eighty percent recycled material, designed to take vials, and a line comprising a Schmucker 12-lane stick packaging machine, a stick inspection system and a cartoner.
This line is designed to process PP-based packaging materials (with and without PE) such as 100% recyclable mono-material plastics like OPP or BOPP with a metallised intermediate layer. Due to its suitability for food contact, this material is a worthy polyolefin-based substitute for the classic PET/ALU material for production of high-barrier flexible packaging.
Last but not least, the area dedicated to green solutions contains a new, versatile machine model which uses only cardboard as packaging material: it can serve as a case packer for small sizes, eliminating the need for plastic bundles, or as a cartoner for large sizes.
The sustainability of packaging materials is only one of the many frontiers in which Marchesini Group is investing in order to comply with the paradigms of the circular economy: it is also engaged in other activities such as the business of Rinova, the company created to give new life to pre-owned original Marchesini lines and machines. In fact, through a remanufacturing process the Group is able to offer customers a solution more advantageous in both economic and environmental terms, with the same quality and reliability specifications.