Corporate
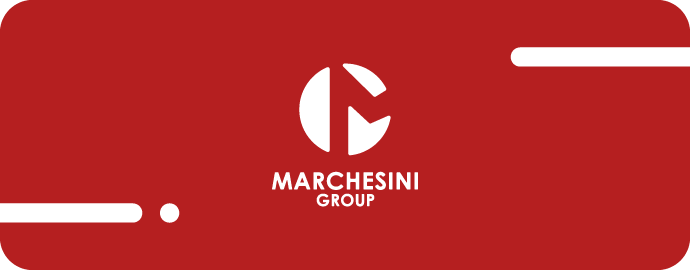
To be able to work with our customers, be they a small producer or a Big Pharma enterprise, we have to keep astride of all the aspects of Industry 4.0, because these companies have been promoting this topic for years, as it affects them strongly. Industry 4.0 is not a mere trend of the times, but a real movement that started back in 2003 and that is now seen in the processes and the finished products.
Maurizio Marchesini, President of the Marchesini Group, said:
The simplest way to explain Industry 4.0 is “digitalised manufacturing”, even if several of its concepts are still not so easy to comprehend or apply.
In terms of the process, we exploit the algorithms resulting from dynamic analyses of management data, which we use to obtain specific information about a certain machine. We are leaders in Cyber Security, since we safeguard our computerised systems through encrypted channels for sensitive information and anti-intrusion software.
The most interesting aspect however involves the 3D printers integrated into the production process. We have recently inaugurated a new rapid prototyping department to build plastic and metal parts, as well as combined plastic-rubber parts, used both on the production line and as prototypes. This department will become the throbbing heart of Industry 4.0 at Marchesini, which already has three-dimensional printers working 24/7 connected inline and programmable from our offices. This special equipment allows us to develop machine components, such as the casing of the robots and the pucks, to control times and costs and to monitor production, machine wear and tear and error management, without using a single sheet of paper. These machines also enable us to prototype the samples very quickly to then produce them with a tested application. This is why our R&D department is so efficient.
In terms of the product, the in-house development and use of robotic arms devised specifically for packaging and capable of adapting themselves to the vastness of the different types of pharmaceuticals commissioned, we are able to speed-up production enormously. Thanks to these robots, our machines are able to manage the product flow, starting upstream, for example with the pill that is inserted into the blister, finishing downstream, where the blister is placed into its box.
The cameras integrated into the new-generation machines guarantee utmost flexibility in managing the various products and materials to be packaged. In our specific case, these cameras are used within the serialization systems to apply unmistakeable codes on each package in order to recognise, trace and identify it. We are leaders in developing production data analyses to be able to predict maintenance needs or the so-called “predictive maintenance” operations, but also in teach-in systems, namely software that automatically optimises the packaging process.
Calderino is a tiny fraction of the municipality of Monte San Pietro near Bologna. It is here, amidst the hills of Sasso Marconi, that a “different” kind of factory compared with all the others of the Marchesini Group works full speed ahead. Instead of blister or carton packaging machines, it makes size-parts and special components, but what makes it different is the equipment it uses.
In addition to the traditional machinery for aluminium, plastic and steel, this company in Calderino uses truly unique equipment. It exploits laser machines to cut into panels to avoid the formation and build-up of dust and to guarantee they meet GMP standards. It has a machine to build the cams too. This project, which was fulfilled in collaboration with the University of Bologna, will improve the quality of the production process because it creates a case-hardened, flaw-free and ready-to-use cam starting from a semi-processed part.
Calderino is also home to our “Fast Format Maker” technologies, similar to rapid prototyping systems, which allow us to consign finished, tested and ready-to-use spare parts very shortly after their order. Their operating mechanism is complex but backed by well-established modus operandi. Each spare part ordered is personalised starting from its standard parameters. The drawing is created in Carpi, or in any one of our other facilities, and sent to Calderino without ever touching paper. Here, it is cast, labelled and associated with the program that will trigger the rapid production systems.
These programmed machines work 24/7 self-sufficiently simply by following the instructions and the priorities given to them. The secret lies in the operating software program, which is what puts us ahead of our rivals, also in the management of spare parts.