Corporate
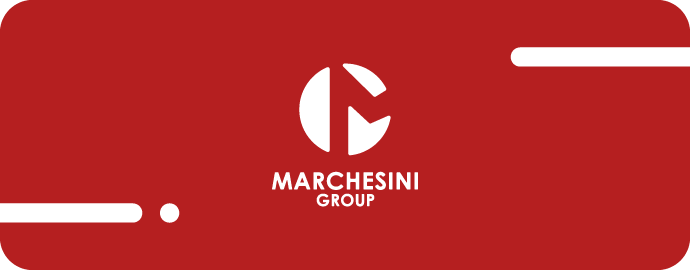
A Mexican customer, specialised in the production of pharmaceuticals for patients with neurological or psychiatric disorders, came to Marchesini Group with a request for a line able to inspect and assemble pre-filled syringes. This line, which has just been shipped, represented a complex project which was completed with success after two years of redesigns. The result is extraordinary, however, in part because it sees a machine from CMP Phar.ma (the Marchesini Group company specialised in solutions for the inspection and control of pharmaceuticals) alongside one from Corima, the Group’s division responsible for manufacturing lines for aseptic packaging of drugs such as Covid-19 vaccines.
The tie-up between the Group’s two brands opens the way for a series of increasingly more complete lines for the inspection and handling of products such as pre-filled syringes and vials, which are increasingly central to the production requirements of companies in the pharma sector.
The first Marchesini Group machine in the line is the SA12J inspection machine by CMP Phar.ma, whose job is to inspect the syringes placed on a conveyor belt by a Pick and Place robot, which has previously taken them from tubs, each containing 160 pre-filled syringes, which are loaded by hand.
The SA12J is specifically designed to automatically perform visual impurity inspection of syringes, rejecting those with various types of defects so that the syringes which are passed as “good” are of irreproachable quality.
Inspection of the syringes is performed by video cameras in six successive independent inspection stations: in each, the product is rotated at a variable speed (up to 3,000 rpm) in front of the camera.
The inspection process begins with the control of the flange by camera TV1. Syringes with defects of the flange (cracking, chipping, breakages, etc.) are rejected. The intact syringes are then fed into the main inspection turret, the heart of the system, before undergoing inspections in the subsequent stations.
Here, cameras TV2 and TV3 carry out particle inspection, rejecting syringes which contain any extraneous particles (glass, hairs, etc.).
Camera TV4 performs a dual task: a third particle inspection and checking the correct filling level of the syringe, by acquiring the position of the surface of the liquid following rotation.
The syringes are rotated at high speed in front of the three cameras TV2, TV3 and TV4 (3,000 rpm), before being brought to a sudden stop: this means that the movement of any particles contained in the liquid is highlighted, allowing the cameras to detect them.
In the next inspection station, camera TV5 checks the presence and correct positioning of the stopper, as well as any liquid which has leaked between the ribs of the stopper.
Camera TV6 checks that the syringe’s security seal is correctly positioned and inspects the aesthetic appearance of the syringe body. Finally, camera TV7 repeats the control of the flange by camera TV1.
All rejected syringes are collected in dedicated containers for different defect types. This allows for a precise summary of the frequency of the various defects during final reconciliation in order to make upline changes so as to reduce/eliminate the causes during the syringe filling phase.
The syringes which pass these tests continue on to the next step, performed by the Corima Combi 1/2 PL machine, which is designed to assemble disposable syringes (plunger insertion) and to label them with self-adhesive wraparound labels.
The Combi performs two further product inspections, checking for the presence of the syringe and needle cover. If both checks are passed, plunger insertion is performed by a turret equipped with ten gripping and screwing clamps. Subsequently, a new sensor checks the plunger-cap combination before the syringe moves on to the labelling section, which is responsible for printing the variable data (batch number and expiration date) on the label. Finally, software written by our partner SEA Vision checks the variable data during the quality control phase.
We are able to provide pharmaceutical companies around the world with the best solutions in the field of aseptic filling, inspection, labelling and packaging of vials and syringes containing vaccines.
Some product lines have already been used in the production of anti-COVID-19 serums: a major Russian biotechnology company, Biocad of Saint Petersburg, is using a Marchesini Group line to produce the Sputnik V vaccine at a rate of 200 vials per minute. And that’s not all. Projects in Latin America are also progressing with the shipping of CMP Phar.ma machines to a Mexican client who will use them in the packaging process for the AstraZeneca vaccine.
We are able to provide pharmaceutical companies around the world with the best solutions in the field of aseptic filling, inspection, labelling and packaging of vials and syringes containing vaccines.
Some product lines have already been used in the production of anti-COVID-19 serums: a major Russian biotechnology company, Biocad of Saint Petersburg, is using a Marchesini Group line to produce the Sputnik V vaccine at a rate of 200 vials per minute. And that’s not all. Projects in Latin America are also progressing with the shipping of CMP Phar.ma machines to a Mexican client who will use them in the packaging process for the AstraZeneca vaccine.