Corporate
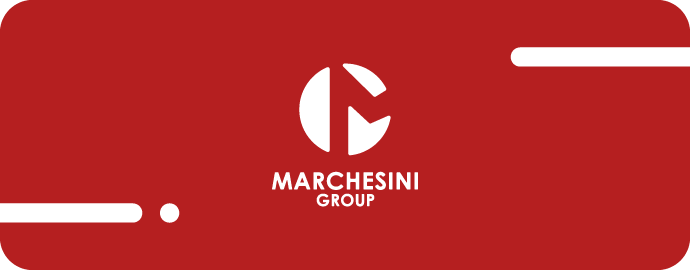
Towards the end of 2020 Catalent, a major U.S. contract manufacturing company with a global network of locations including Italy, contacted us to help with a unique challenge. The company was in the process of upgrading existing filling lines at their Anagni site to better support filling of biologic products in aseptic conditions. In response to the growing demand for biologics and vaccines, the company, headquartered in Somerset (New Jersey, USA), decided to accelerate their plans and convert an existing production line into a filling line under isolator for biological products, capable of producing tens of thousands of vials per hour in aseptic conditions.
The project - given the name x-BIO - was formally launched at the end of 2020. It marked the start of a race against time, with two complex objectives: to adapt the new technologies to the inside of an existing production department and, above all, to install the line safely in an exceptionally short time, enabling starting of factory acceptance testing (FAT) within six months.
To manage this, Corima, the Marchesini Group brand that leads the field in the construction of aseptic filling machinery and lines, rewrote its production plans to prioritise the Catalent project. Thanks to a very close partnership with Catalent and weekly project management reviews, the line, including the isolator and the air treatment system, was completed on schedule, with FAT in July 2021, followed by site acceptance testing (SAT) in October, and subsequent Regulatory Agency approval planned for the early months of 2022.
“We managed to meet deadlines we would have considered impractical before the pandemic: construction of a liquid filling line with isolator in just over six months, and seeing it go into operation within a year,” stated Pietro Cassani, CEO of Marchesini Group. “Our hope is that these technologies will speed up production of biologics and vaccines, helping to bring more and more life-saving medicines to patients on a global scale”.
“Catalent has been a leader in biologic manufacturing, and when the pandemic began, we looked for ways to accelerate our investments to help meet the need for capacity,” commented Barbara Sambuco, Vice President, Drug Products Operations, Catalent Biologics. “In completing this project safely and in an unprecedented time, the Marchesini Group helped us again live up to our patient first commitment - which is to focus on patient safety, impact, and outcomes in all that we do - for COVID-19 vaccines and the many other important medicines that we manufacture".
The line - comprising a Stery-LC filling/stoppering machine and a Capsy-LC capping machine - was designed to be extremely flexible, thanks to the use of peristaltic pumps combined with disposable transfer and storage systems. This type of technology minimises technological transfer times, especially those required for cleaning validation. The line is also able to fill products via rotary piston pumps combined with an in-place cleaning and sterilisation (clean-in-place/sterilization-in-place) system, the procedure typically used for the batch production of biological products.
In both cases, the automatic robotised weight checking system (industrial personal computer (IPC) system) ensures monitoring and certification of dosing precision.
Thanks to its “balcony style” technology, the Stery-LC filling machine guarantees both a safe accessibility to all critical zones via the gloves, and complete clean integration with the isolator. This optimises the unidirectionality and uniformity of the laminar flow and provides complete separation between the working area and the mechanical zone, located in the rear of the machine. With this layout, most of planned and unplanned corrective maintenance activities can be performed even without accessing the controlled contamination areas.
Once filled, the vial is then capped inside the Capsy-LC. The filling machine isolator has its own heating, ventilation, and air conditioning (HVAC) system for external air treatment, filtration and exhausting, as well as a vapour hydrogen peroxide (VHP) system for the sterilisation of all exposed surfaces.
Catalent is the global leader in enabling pharma, biotech, and consumer health partners to optimize product development, launch, and full life-cycle supply for patients around the world. With broad and deep scale and expertise in development sciences, delivery technologies, and multi-modality manufacturing, Catalent is a preferred industry partner for personalized medicines, consumer health brand extensions, and blockbuster drugs.
Catalent helps accelerate over 1,000 partner programs and launch over 150 new products every year. Its flexible manufacturing platforms at over 50 global sites supply over 70 billion doses of nearly 7,000 products to over 1,000 customers annually. Catalent’s expert workforce exceeds 19,000, including more than 2,500 scientists and technicians. Headquartered in Somerset, New Jersey, the company generated $4 billion in revenue in its 2021 fiscal year.
For more information, visit https://biologics.catalent.com/