Corporate
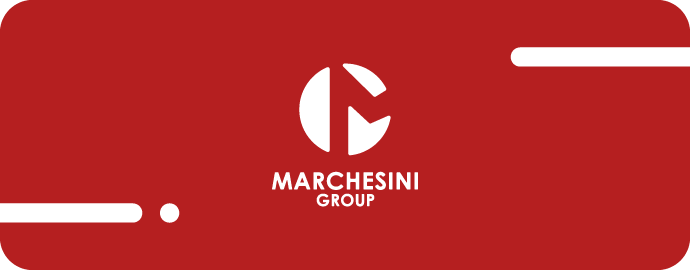
One of Italy’s most innovative, fastest-growing players in the low-dose medicine, medical device, nutraceutical, dermocosmetics and Bach Flowers sectors contacted Marchesini Group for the purchase of a line for the aseptic atmosphere packaging of vials containing homeopathic products for injection.
The line - developed by Corima, at the Italian state of the art for the aseptic filling of sterile products - is able to wash, dry, sterilise and then fill and cap vials.
Unlike standard lines, it also includes a product formulation system using mobile tanks with the relative cleaning-in-place and sterilisation-in-place (CIP/SIP) for automated, repeatable, validated management of the cleaning and sterilisation of all parts in contact with the product.
A WR series washing machine installed upstream of the line ensures perfect cleaning of vials both internally and externally, through blowing with filtered compressed air, pre-washing with recycled water and final rinsing with Water for Injection (WFI).
After washing, vials pass through the DEPYR laminar flow depyrogenation tunnel. Created by Corima in partnership with Neri, this modular tunnel protects, sterilises and cools vials and can be constructed in different sizes to meet all production requirements.
Once sterilised, vials move on to the Stery, a continuous linear filling and capping machine for the aseptic filling of vials of various sizes up to 100 ml.
The Stery delivers a number of advantages compared to a conventional room-centre layout, specifically:
Thanks to these characteristics, Stery is able to comply in full with the Regulators’ requirements for injectables and in particular with the new EU GMP Annex 1, which enforces the minimisation or elimination of maintenance procedures inside clean rooms.
Once filled, vials move on to the Capsy for capping. This machine’s compact size is fundamental in reducing the time vials take to pass from the filling to the capping zone.
The cap pre-feeder allows the hopper to be supplied directly from the sterile bags on the operator side, with no further steps required.
The Capsy delivered to the customer features an update to the capping head which provides improved quality and a more attractive result when using flip-off caps. The stainless steel capping head also undergoes an innovative hardening treatment which allows it to be sanitised without any detriment to its stainless qualities or its working lifetime.
The capping system controls both the compression pressure applied to the cap (by means of a proportional regulator) and the speed at which the cap rotates on the blade (by means of a brushless motor) to provide a perfectly repeatable process.
The end result is a compact, efficient machine, designed to facilitate installation against a wall and guarantee the user safety in use and the potential for integration with feeding systems, buffers and loading and unloading units for freeze-dryers, capping machines, a rotary table and a double tray packaging machine.